Table of contents:
Knife Geometry vs. Plastic Melt-Flow Index Correlations
Smart Pusher-Ram Settings to Avoid Bridging and Improve Dwell Time
Screen Size Selection for Target Flake Dimensions
Inline Conveyor Integration to Maintain Constant Shredder Feed
Unlock the Full Potential of Your Single Shaft Shredder
Knife Geometry vs. Plastic Melt-Flow Index Correlations
Knife geometry plays a pivotal role in shredding efficiency across various types of materials. The melt-flow index (MFI) of plastic refers to its capacity to flow at high temperatures and provides a guideline for determining optimal knife angles and configurations. For high-MFI plastics like polyethylene (PE) and polypropylene (PP), sharper knife angles and softer cutting profiles enhance precision and ensure clean cuts without deforming the material structure. Conversely, for low-MFI plastics such as vinyl (PVC), robust blades with higher durability are ideal for preventing excessive wear while maintaining shredding consistency. Blade materials and configurations also matter greatly. High-alloy materials like CrMoV steel are recommended for their resistance to wear, effectively enduring the abrasive properties of plastics. The proper alignment of "V" configuration rotary blades combined with adjustable fixed blades not only maximizes the shredding process but also optimizes the machine’s ability to handle harder and more complex plastics.
Smart Pusher-Ram Settings to Avoid Bridging and Improve Dwell Time
Achieving a seamless shredding flow involves controlling the pusher-ram system, which is responsible for feeding materials into the cutting chamber effectively. Improper settings can result in bridging, where the feed material blocks the shredder inlet, causing operational downtime. To avoid bridging, adjust the hydraulic system of the pusher-ram so that materials are fed steadily at a pace that prevents rotor overload. Intelligent hydraulic controls are an essential feature, allowing for speed adjustments based on the feed material's density. When processing breakable materials, faster pusher speeds should be utilized. For tougher and heavier materials, slower pusher movements are recommended to prevent excessive strain on the rotor. Additionally, reinforcing the base plate minimizes the impact of heavy materials, preserving the machine’s structural integrity over extended operations.
Screen Size Selection for Target Flake Dimensions
The granule size produced by single shaft shredders is determined by the screen mesh size. Selecting the appropriate screen size is paramount for meeting industry standards and optimizing end-use applications. Mesh sizes typically range from 40mm to 100mm, depending on the requirements for further material processing. For applications requiring finer outputs, such as reprocessing PET flakes into fibers or resins, smaller mesh sizes ensure uniformity and consistency. On the other hand, recycling HDPE or larger plastic parts requires coarser dimensions that allow for quicker throughput without compromising material quality. Ensure the mesh screen is adequately maintained; periodic inspections and replacements are necessary to sustain shredding efficiency and guarantee operator safety during screen changes.
Inline Conveyor Integration to Maintain Constant Shredder Feed
A steady flow of materials into the shredder is crucial for maintaining optimal throughput. Integrating inline conveyors can resolve feed inconsistencies while reducing manual intervention. By automating the material supply, conveyors deliver a continuous stream of plastics to the machine, reducing idle times and maximizing productivity. Customizing conveyor speeds to match the specific shredding parameters of your single shaft shredder ensures consistent material input. Furthermore, equipping the conveyor with sensors to monitor and automatically adjust feed rates prevents rotor overload and maintains a balanced workflow. This integration also safeguards against material buildup around the cutting chamber, promoting smoother operations over extended periods.
Unlock the Full Potential of Your Single Shaft Shredder
Optimizing your single shaft shredder for mixed plastics involves fine-tuning key components, from the knife geometry to the feed system. By employing intelligent hydraulic controls, selecting appropriate screen sizes, and integrating supporting equipment like inline conveyors, your operation can achieve higher efficiency, reduce downtime, and extend the lifespan of your shredder. For businesses seeking advanced solutions, single shaft shredder manufacturers like Soyu Machinery provide innovative machines tailored to diverse industrial needs. Their state-of-the-art designs, featuring highly durable blades, precise hydraulic control systems, and customizable configurations, make their machines the perfect choice for tackling even the most challenging recycling tasks.
By taking a strategic approach to machine optimization, businesses involved in plastic recycling can not only boost throughput but also enhance material quality. Adopting these best practices ensures that single shaft shredders operate at peak performance, paving the way for sustainable and efficient recycling processes.
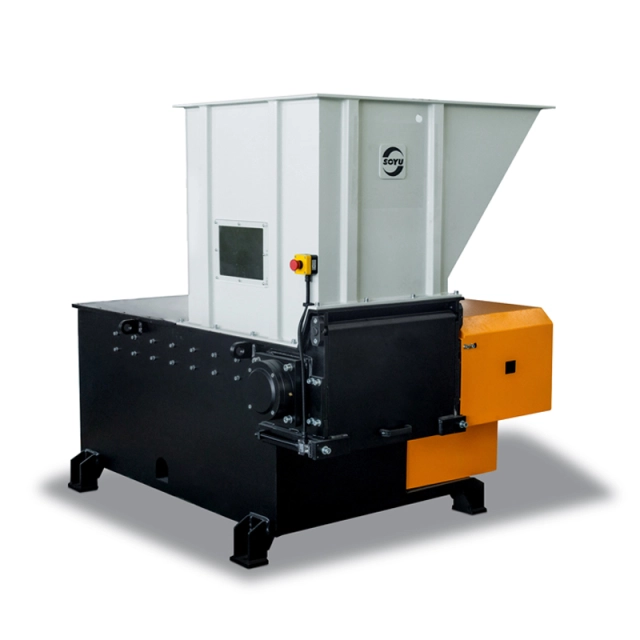
No comments:
Post a Comment